eSmart Systems and envelio are excited to announce their partnership to support utilities with their asset management and grid planning decisions.
eSmart Systems’ Grid Vision® solution powered by AI enables utilities to scale virtual inspections and grid inventory while digitalizing transmission and distribution assets with an image-based digital asset, combining inspection data, substation assets, metadata and grid topology to provide actionable insights and downstream value beyond the inspection.
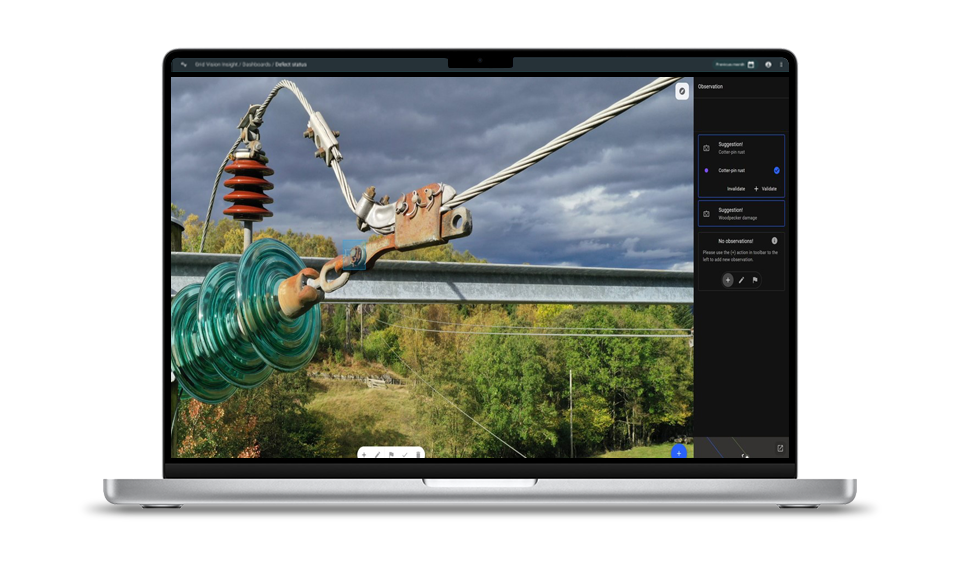

envelio’s Intelligent Grid Platform empowers utilities by delivering a digital twin of the distribution grids. The platform unites relevant grid data from multiple sources into one platform to digitalize and automate grid planning and grid operation processes. Applications like Grid Planning and Grid Study enable the evaluation of future scenarios and their effect on the power grids. The results can then be used for strategic grid planning.
Bringing the two solutions together unlocks a powerful combination of an accurate image-based digital asset with the digital twin, resulting in a knowledge-based platform to support utilities to break down silos between grid operations, investment planning and condition monitoring to provide holistic and accurate information on the conditional and physical state of the grid. Based on these additional insights on the power flow and mechanical asset data combined, utilities can enable improved maintenance and inspection planning, support unplanned outage response and improve long term asset investments and strategic grid planning for their power grids.
The partnership between eSmart Systems and envelio will enable a giant leap in the cross-functional use of data from both our worlds. This will benefit multiple departments and user groups within the utility, due to the exchange and uplift of the different types of information we each focus on.
Innovation partnerships like the one with eSmart Systems are the key to the energy transition. Together we create a solution with a technological best-of-breed approach that enables cost-optimized and accelerated asset management and expansion planning of the power grids and thereby supporting grid operators in meeting the challenges of the energy transition.
- Inspektionsdienstleistungs-Programm zur Bereitstellung einer vollständigen virtuellen Inspektion des AllgäuNetz Freileitung Hochspannungsnetz.
- Virtuelle Inspektion unterstützt durch Künstliche Intelligenz.
Die AllgäuNetz ist Verteilnetzbetreiber im südlichen Allgäu in Deutschland. Gemeinsam mit eSmart Systems beginnt AllgäuNetz die Zusammenarbeit mit dem Ziel die Inspektion des Freileitungsnetzes deutlich zu verbessern. Die Lösung der eSmart Systems ermöglicht eine virtuelle Inspektion der Freileitungen, die durch eine künstliche Intelligenz unterstützt wird.
Mit diesem Schritt unterstreicht AllgäuNetz ihre Strategie, verstärkt erneuerbare Energien zu integrieren, den Ausbau intelligenter Netze auszudehnen und die Digitalisierung ihrer Assets und Prozesse voranzutreiben. Dies dient dazu, die Energiewende zu unterstützen und gleichzeitig das hohe Maß an Versorgungssicherheit für die AllgäuNetz Kunden zu optimieren.
Wir waren sehr beeindruckt vom Ansatz und der Methodik von eSmart Systems zur Unterstützung unserer Inspektionsanforderungen. Im Rahmen eines ersten Pilotprojekts lieferten die qualitativ hochwertigen und präzisen Inspektionsergebnisse, die im Rahmen von Grid Vision® bereitgestellt wurden, wertvolle Einblicke in unsere kritische Infrastruktur. Wir freuen uns, dies nun in unserem gesamten Hochspannungsnetzbetrieb in dieser Qualität durchführen zu können.
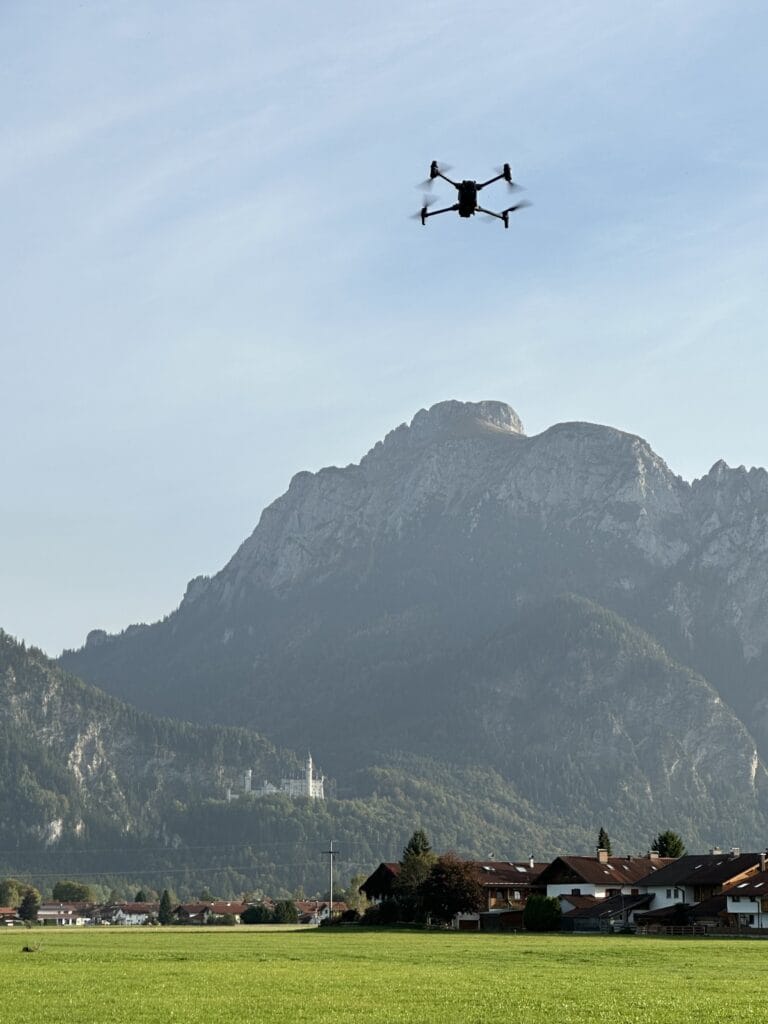
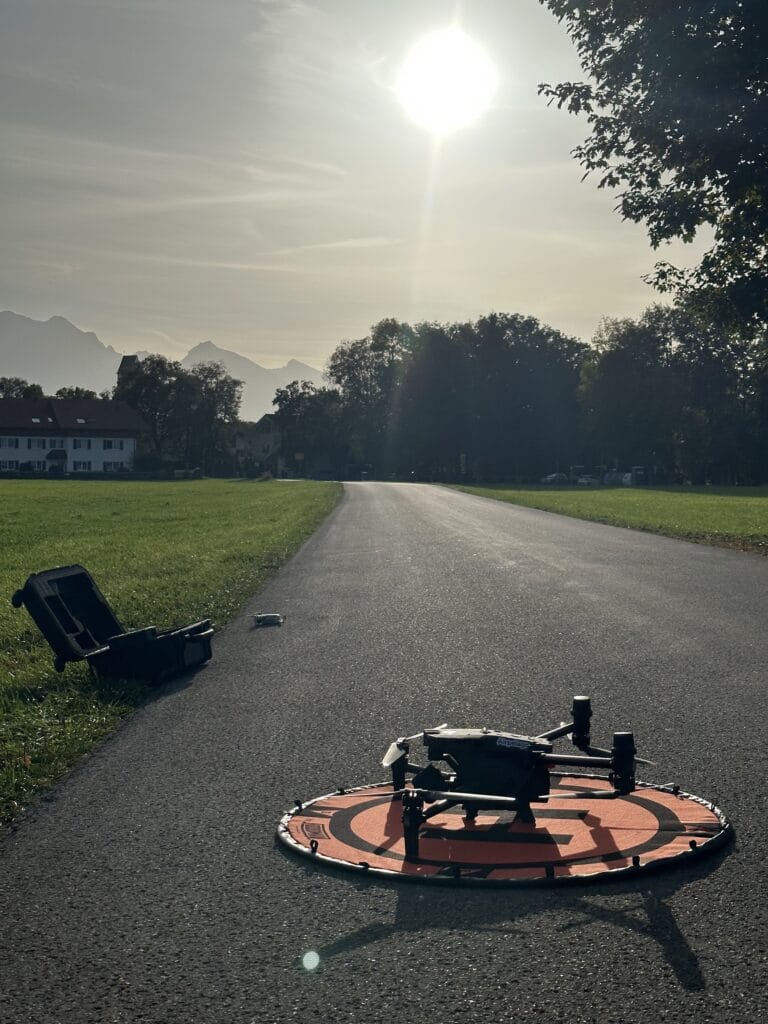
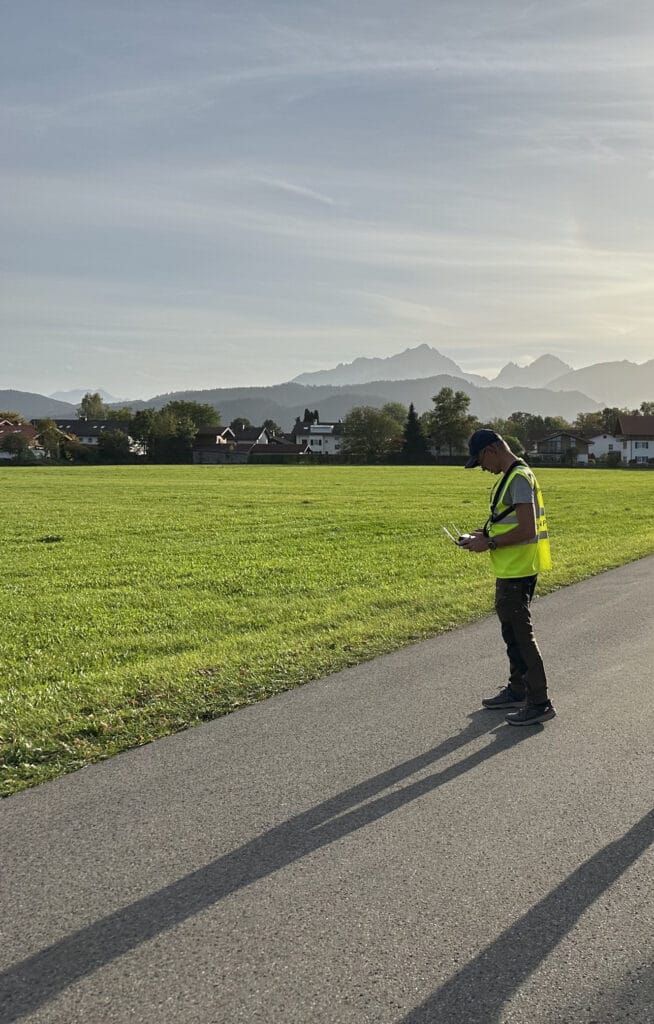
Im Rahmen dieser Partnerschaft bietet eSmart Systems eine vollständige Ende-zu-Ende-Inspektionslösung von der Bilderfassung mit Drohnen und automatisierten Flugmustern bis hin zur virtuellen Inspektion mit Grid Vision®. Somit erhöhen wir die Inspektionseffizienz. Diese Partnerschaft wird sicherere, genauere und effizientere Sichtprüfungen der Freileitungen ermöglichen und die Inspektionskosten optimieren. Zusätzlich wird das Programm ein bildbasiertes digitales Abbild der Freileitungsanlagen erstellen, welches die AllgäuNetz dabei unterstützt, sich bei der Investitionsplanung auf Betriebsmittel, basierend auf ihrem Zustand, für Wartungs- und Reinvestitionsmaßnahmen zu konzentrieren.
The partnership between eSmart Systems and envelio will enable a giant leap in the cross-functional use of data from both our worlds. This will benefit multiple departments and user groups within the utility, due to the exchange and uplift of the different types of information we each focus on.
Über die AllgäuNetz GmbH & Co. KG
Die AllgäuNetz GmbH & Co. KG ist der Verteilnetzbetreiber im südlichen Allgäu und versorgt 144.000 Kunden sicher mit Strom.
Eine sichere und zuverlässige Stromversorgung ist eine wichtige Grundlage unserer Gesellschaft. AllgäuNetz GmbH & Co. KG, als Allgäuer Unternehmen Kraftwerke GmbH, Allgäuer Überlandwerk GmbH, Energiegenossenschaft z.B. Mittelberg, Energiebedarf Oberstdorf GmbH und Energiebedarf Oy- Kressen eG stellt sich dieser Verantwortung konsequent.
Mit unseren Mitarbeitern sind wir für große Teile des Stromnetzes im südlichen Allgäu verantwortlich. Das in Betrieb befindliche Stromnetz umfasst ca. 5.500 km Leitungen auf einer Fläche von ca. 1.700 km².
Durch das Zusammenspiel erneuerbarer Energien, intelligenten Netzausbau und -betrieb sowie zuverlässige flächendeckende Betreuung sorgen wir für ein hohes Maß an Versorgungssicherheit.
Gemeinsam mit unseren Privatkunden, Gewerbebetrieben und den Gemeinden im südlichen Allgäu arbeiten wir täglich an der sich verändernden Energielandschaft und setzen die Veränderungen gemeinsam innovativ und zielorientiert um.
Über eSmart Systems
eSmart Systems ist ein führender Anbieter von KI-gestützten Lösungen für die Inspektion und Wartung kritischer Infrastrukturen. Mit unserer Softwarelösung, Grid Vision® revolutionieren wir die Betriebs- und Wartungsprozesse von Netzbetreibern für ihre Übertragungs- und Verteilungsnetze. Wir unterstützen Netzbetreiber weltweit dabei, Inspektionskosten zu senken, Inspektionen sicherer zu gestalten, die Qualität der Asset informationen zu verbessern und die Lebensdauer der Assets zu verlängern.
- Inspection as a Service program to deliver full virtual inspection of AllgäuNetz’s distribution network.
- Virtual inspection supported by Artificial Intelligence.
AllgäuNetz the Distribution System Operator in southern Allgäu, Germany is partnering with eSmart Systems to transition their infrastructure inspection from manual to virtual inspection supported by Artificial Intelligence. This move is to emphasize AllgäuNetz’s strategy of integrating more renewables and expanding their intelligent networks and digitalizing their assets and operations to support the energy transition and optimise a high level of security of supply to their customers.
Wir waren sehr beeindruckt vom Ansatz und der Methodik von eSmart Systems zur Unterstützung unserer Inspektionsanforderungen. Im Rahmen eines ersten Pilotprojekts lieferten die qualitativ hochwertigen und präzisen Inspektionsergebnisse, die im Rahmen von Grid Vision® bereitgestellt wurden, wertvolle Einblicke in unsere kritische Infrastruktur. Wir freuen uns, dies nun in unserem gesamten Hochspannungsnetzbetrieb in dieser Qualität durchführen zu können.
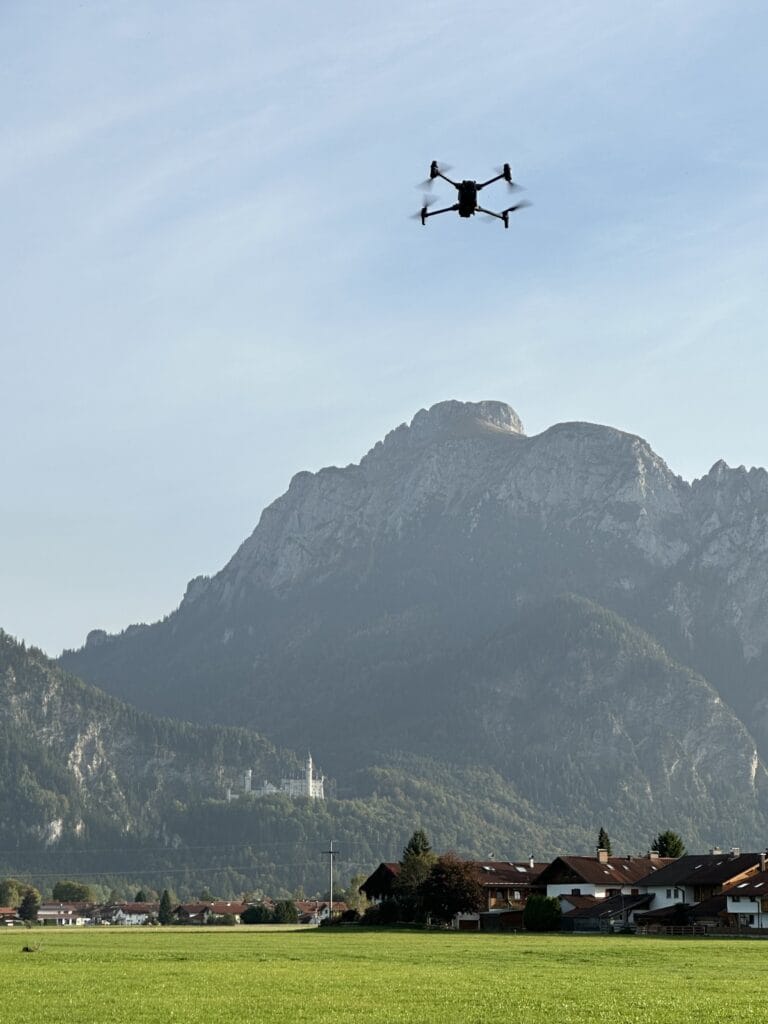
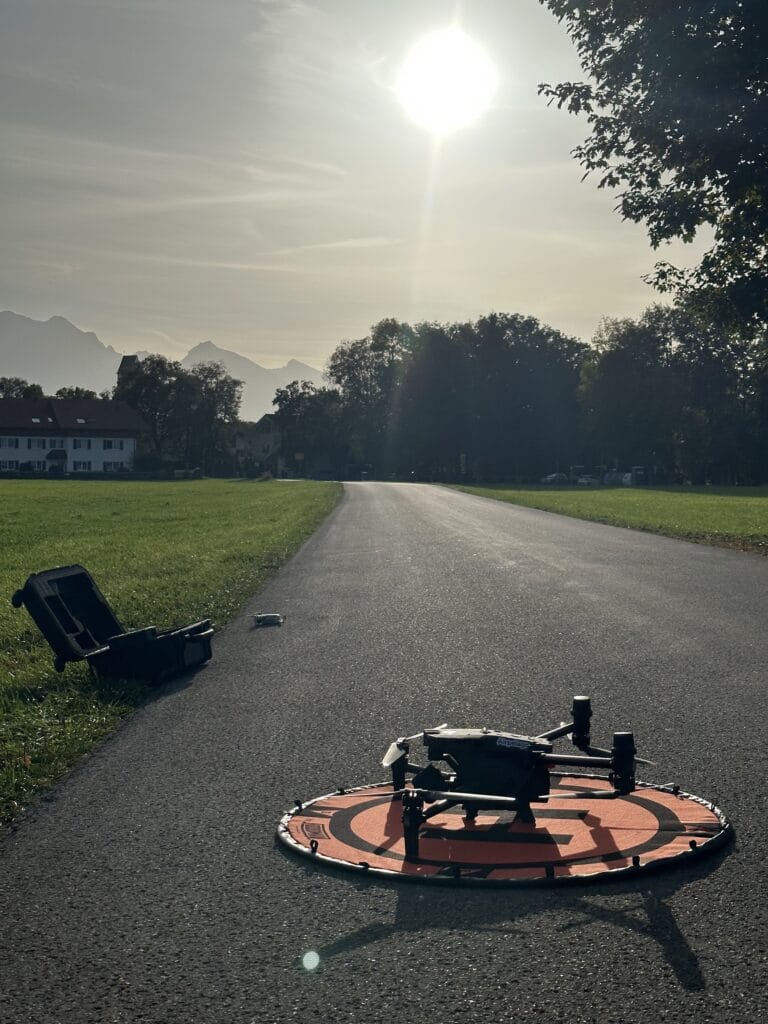
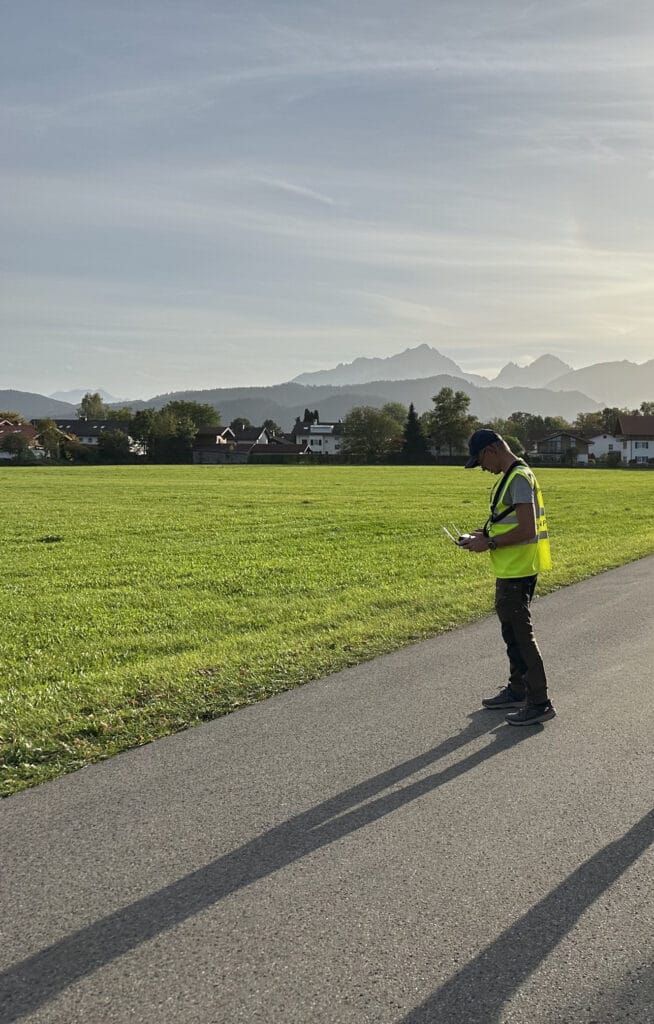
As part of this partnership eSmart Systems will provide the full end-to-end inspection solution from image capture with automated flight patterns and drones to the virtual inspection, which will provide safer, more accurate and efficient visual inspections and will optimize the inspection costs. The program will also build an image-based digital asset alongside the inspection which will support AllgäuNetz to focus on assets based on condition for maintenance and rebuilds.
The partnership between eSmart Systems and envelio will enable a giant leap in the cross-functional use of data from both our worlds. This will benefit multiple departments and user groups within the utility, due to the exchange and uplift of the different types of information we each focus on.
About AllgäuNetz GmbH & Co. KG
AllgäuNetz GmbH & Co. KG is the Distribution System Operator in southern Allgäu, Germany, supplying safe and secure electricity to 144,000 customers.
A safe and reliable power supply is an important basis for our society. AllgäuNetz GmbH & Co. KG, as a company belonging to Allgäuer Kraftwerke GmbH, Allgäuer Überlandwerk GmbH, Energiegenossenschaft eG Mittelberg, Energiebedarf Oberstdorf GmbH and Energiebedarf Oy-Kressen eG, consistently faces up to this responsibility.
With our employees, we are responsible for large parts of the power grid in southern Allgäu. The power grid in operation includes approximately 5,500 km of lines in an area of approximately 1,700 km².
Through the interaction of renewable energies, intelligent network expansion and operation as well as reliable support across the area, we ensure a high level of security of supply.
Together with our private customers, commercial businesses and the communities in southern Allgäu, we work daily on the changing energy landscape and implement the changes together in an innovative and goal-oriented manner.
About eSmart Systems
eSmart Systems is a leading provider of AI-powered solutions for the inspection and maintenance of critical infrastructure. With our software solution, Grid Vision® we revolutionize how utility companies operate and maintain their transmission and distribution networks. We support utilities globally to reduce inspection costs, make inspections safer, improve the quality of asset data and prolong asset life. eSmart Systems has more than 20 years of international experience in establishing and operating knowledge-based, leading IT and energy-related companies targeting global markets.

In this whitepaper, learn what to consider and how you can realize the benefits of the new generation of infrastructure inspections and increase the resiliency of your power grid.
The project, completed in 2021, focused on hardware and defects identification. The project looked at cotter pins, with an emphasis on loose and upside-down cotter pins. The project was able to automatically detect over 11,000 total and successfully identify 781 upside-down pins within a few seconds. The project enabled the public utility’s maintenance engineers to efficiently locate the 2-inch upside-down cotter pins on up to 100 feet high towers and assess their conditions. The outcome of the project is an increase in powerline safety, field worker safety, and, as result, community safety. The case-study described below demonstrates the potential of virtual powerline inspections in enhancing community safety.
Introduction
Multiple large-scale wildfires are reported in the US every year. Such events cost tens of billions of dollars in direct costs such as property loss and damage and indirect costs such as long-term health exposures, market loss, and non-collectable taxes, etc[1]. The consequences of such events can be disastrous from a human, material, and environmental perspective.
Defects in the power grid can cause wildfires; active causes can include a tree or branch falling over a powerline and sparking a wildfire. Triggered material or old powerline components can generate arcs or sparks, and under dry weather conditions and with dry surrounding vegetation, can lead to disastrous and hard to control wildfires.
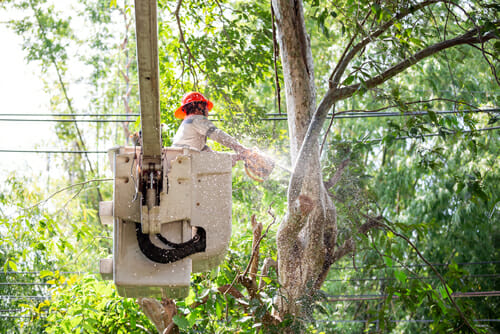
To minimize the risk of wildfires caused by power grid issues, it is important to ensure conductors do not encounter any foreign objects like trees, other conductors, or the ground. This can only be achieved by properly managing vegetation in areas surrounding powerlines and by sufficiently keeping conductors separate from each other. Spacers and cotter pins, specifically, play a critical role in keeping conductors separated. Spacers keep conductors away from each other, while cotter pins hold the parts in transmission towers in place.
Cotter pins, however, could wear out and loosen over time. A loose and upside-down cotter pin is more likely to slip, becoming unsafe and increasing the chance of conductor failure and the probability of generating an arc flash touching their surroundings. Therefore, a main focus of the efforts led by the public utility to minimize the chance of wildfires is the management and maintenance of cotter pins specifically. As they are more likely to be upside-down than loose, the public utility decided to first assess the number of upside-down cotter pins on their grid. However, manually identifying the orientation of cotter pins is a tedious and resource-consuming task, as there can be as many as 50 2-inch cotter pins on each lattice tower, and the grid in this case includes over 1000 lattice towers.
The new approach
Both the public utility and the engineering and construction company defined the inspection process based on the required scope and accessibility of each structure. eSmart Systems shared their expertise to support that process definition and provided access to Grid Vision, a virtual inspection solution for power grids, enabling professionals to inspect powerlines from the office. Virtual inspection is a new approach to conducting powerline inspections by leveraging the power of automation, smart algorithms, and user-friendly interfaces to facilitate the work of the professionals analyzing the status of the infrastructure. Virtual inspections are also supported with artificial intelligence (AI) to automatically and promptly identify all the components of a power grid, as well as to detect various failures in the grid. With the application of such technologies, the software was able to identify 781 instances of upside-down cotter pins out of 11,000 cotter pin crops, within seconds (Figure 1).
Figure 1: Examples of an upside-down cotter pin automatically detected in the grid.

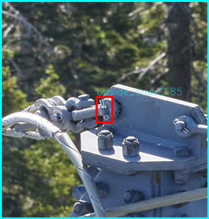
By associating those findings with information of the tower on which the upside-down cotter pins were located, the public utility could identify which towers required attention instantly. This approach has improved the efficiency and accuracy of identifying upside-down cotter pins and improved safety by having line workers only climbing structures when needed.
The utility also looked at other types of key components and their failure modes (flashed insulators, woodpecker damage on wooden transmission towers, rust on lattice towers, etc.) that could be identified utilizing this new approach for a proactive maintenance of powerlines. C-hooks and shackles, which are used for affixing insulators to brackets attached to crossarms, are particularly important components to look at in this context. The lattice towers are over 50 years old. Nonetheless, the virtual detection system was able to identify over 25,000 crops of C-hooks and shackles on the images captured during the inspection and very little wear was detected.
Figure 2: Examples of (a) a c-hook in good condition, (b) very limited level of wear seen on c-hooks during the project and (c) a shackle, highlighting the general good condition of those components in the grid.
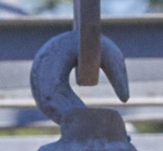
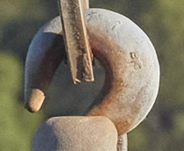
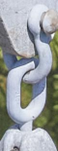
Utilities are constantly looking for innovative ways to improve safety inspection and grid maintenance. This project has demonstrated that well-designed solutions supported by AI are game-changing tools, making inspection easier, more efficient and safer. The collaborative AI approach was instrumental to ensuring the correct components were identified and defects detected. The construction company’s review of the results from eSmart Systems’ Grid Vision solution ensured that high quality inspection standards were met and illustrated how utilities and engineering companies can benefit from virtual inspection tools.
The success of this program demonstrates how proactive actions can be implemented to enhance power grid management efficiency, and proves that smart solutions could help prevent wildfires, in addition to illustrating numerous other advantages, such as new quality assessment possibilities, defect detection standardization, and increased trust in data.
Contact us today and see how Grid Vision is transforming the way the world’s leading energy providers inspect and maintain critical infrastructure.
[1]https://www.nfpa.org/News-and-Research/Publications-and-media/NFPA-Journal/2020/November-December-2020/Features/Wildfire
Not all virtual inspections will give you the same results, so before you go and add virtual inspections to your inspection toolbox, there are some things you need to consider so you get the maximum value.
So, what’s the big plan? Why are you thinking about virtual inspections? Cut costs, be more efficient, enhance safety, try out Artificial Intelligence (AI)? Or all of the above…
A mix of inspection methods such as ground, climbing, bucket truck, routine aerial, and detailed aerial patrols supplemented with advancements in viewing and data collection technologies (e.g., stabilized binoculars, digital cameras, field computers, etc) have been utilized for decades to assess system conditions and identify maintenance items needing mitigation. Maintenance and inspection teams have developed best practices to improve what they get out of these inspection methods, while there are still improvements that can be made, most utilities are quite comfortable with the planning, scope and outcomes of these methods.
Now with virtual inspections, while the objectives are the same, perform a visual inspection of the grid, identify defects, and categorize their priority level so maintenance teams can deploy crews to repair any high priority defects and schedule lower priority maintenance. The methodology, enabling technologies and subject matter experts can have a huge impact on the results from your virtual inspection program.
Getting your planning right!
If you don’t scope and plan your virtual inspections correctly you could end up spending more on these types of inspections with less return, and the CFO really doesn’t like that.
You need to determine what defects your virtual inspection will focus on, as an aerial photo will show you the grid from a different perspective relative to say ground patrol and there will be certain defects that may be more difficult to detect, for example defects at the base of a pole or structure for which the evidence is relatively small. Further, it may not be possible to effectively measure the extent of such a defect from a photo.
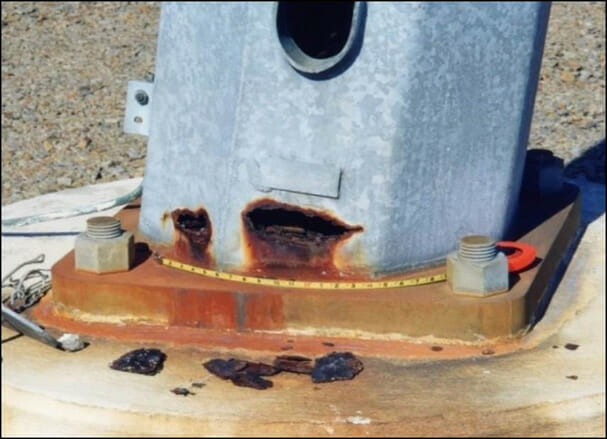
Image taken by foot patrol of corrosion at the bottom of the structure. Difficult to get depth and measurement of defect from a virtual inspection. Image courtesy of EDM International.
Let’s look at data capture.
Think about the number of circuits you are planning to inspect with this method, and the technology you will use to capture the data from the field. Determine if you will be utilizing drones, or manned aircraft and once you determined the method, what will be the flight strategy and profile as this impacts your cost, time and the defects you can detect. For example, if you are utilizing drones (and of course you are because drones are super cool!), you can conduct linear or orbital flight pattern or a combination of both, you can also invest in drone flight optimization software to help optimize your data capture.
And yes, drones are cool and all but have you ever tried flying one? It is not that easy, and it is not always allowed, so you also need to consider regulations and potential flight restrictions in certain areas. Regulations vary from region to region and gaining approvals for certain types of flight can be a long process (government entities are not really known for being quick) especially when seeking to perform Beyond Visual Line of Sight (BVLOS) operations. With data capture the key is to strike a balance between ensuring you get the data you need without needing to re-fly and making sure the approach is scalable.
Or were you planning a totally different approach and want to use images taken by other methods like LiDAR flights – then there are a lot of different questions you should be asking, like will it even work? Technology is rapidly changing and the ability to bolt on capturing LiDAR with what you are already doing will greatly expand the use case for the data and dramatically improve your return on investment.
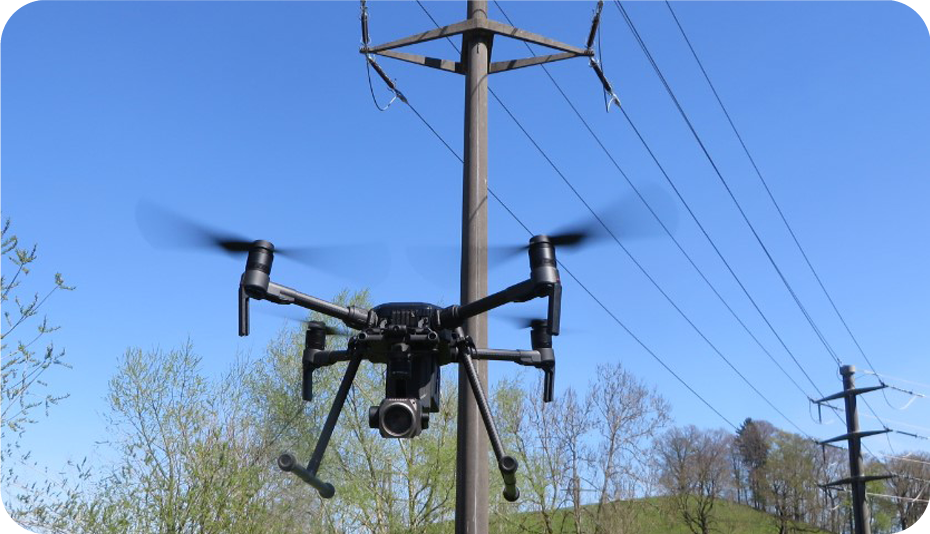
Then there is the image capture technology.
Just like our mobile devices, image capture technology is rapidly advancing. Who thought 15 years ago we would utilize our phones for almost everything and they would replace our wallets and cameras. This begs the question, how do you pick the right technology and ensure that the data you have captured is usable not only for an inspection, but beyond?
Once you capture the data, what are your plans with the number of images and data that you are going to collect, where will you store it all? You have to budget for it and plan for how you will be able to access the data, make it usable so that it is not just left in a data lake (gathering dust and eventually turning into an unstructured data swamp with warning signs) until the next inspection.
We’re conducting an ongoing large-scale virtual inspection program and over just the first three-years we’ve collected so many images that if we were using printed images (we’re not 😉), and we stacked them on top of each other they would equate to the height of the Empire State Building (that is 380 meters without the spire and antenna)! So, storage, albeit electronic/digital, is definitely something to think about.
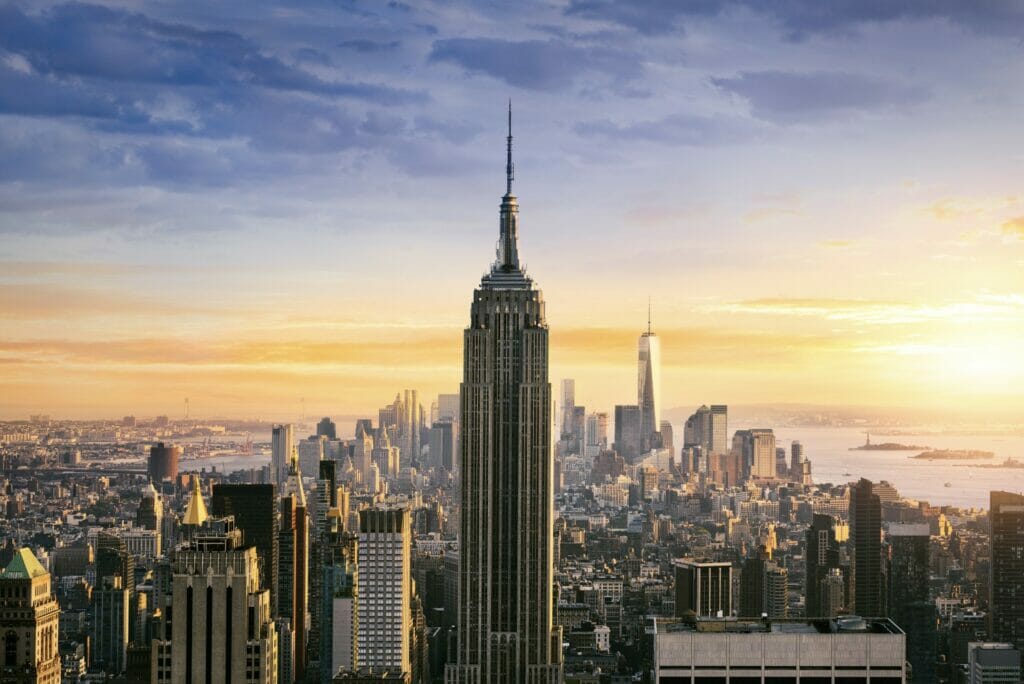
The technology to enable virtual inspections and processing of the inspection data is something that needs to be given a lot of thought. There are a lot of solutions on the market at the moment, how do you pick the right one for you? Do you know what you need? Do you know what questions you should be asking to get beyond the smoke and mirrors of an impressive demo? A couple of important points to consider…
- Can the software structure your images based on asset models?
- Can it also link the images to the metadata, and the right physical asset on the grid?
- Does the software you are considering enable efficient inspection and recording of findings?
- Does this software facilitate fast loading times for memory intensive images and quick access for inspectors? Time is money, everyone knows that.. right?
Then there is advanced technology like AI.
The new shiny tool in the toolbox, that is being marketed as the solution to all your problems. How do you build your strategy around that? One of the most important points to consider is that AI, no matter what industry you are in, needs training data (and a lot of it!). Therefore, when you are seeking an AI solution or trying to build your own, know that there are a lot of utilities who tried before you, and are now stuck with their AI in the innovation stage; because their AI will not do what they expected, it won’t solve all their problems because they simply do not have enough data to train the AI to detect the defects and components. The CFO is now cutting their budget since they are not showing any results, and they’ve had so many developers working on it that the costs have skyrocketed.
So instead of being put in that awkward position, know that AI solutions are complex and take time to develop, and they are surrounded by expectations and misconceptions. Our personal favorite is that AI will replace the Subject Matter Experts (it won’t, we promise) so managing the expectations are key. Any transition takes a little time, and Rome was not built in a day – remember?
The Subject Matter Experts.
Let’s pretend we have all that. Once you have plans for the scope, capture process and technology, the next question is – who will perform the virtual inspection? Your Subject Matter Experts (SMEs) will have the biggest impact on the value you get back. And thus it is critical to consider their experience and expertise and ensure they are trained on the technology…which needs to be easy to use and efficient, or your SMEs will quickly become disenchanted.
Planning does not end with the inspection.
If you do not incorporate consideration of the additional business processes associated with inspection work into your planning, then your return will be short lived and the value limited. We have seen utilities do this right and when they do, we find maintenance teams consistently utilizing the inspection data in their everyday work; being able to do a lot more without a field visit. Accurate inspection data can empower utilities to prioritize capital projects and save a ton of money by only focusing on assets that need to be prioritized.
There have also been instances where maintenance teams have been able to reduce the risks of unplanned outages by identifying at-risk assets utilizing accurate virtual inspection data and enhance safety, reduce costs and help ensure compliance with their own standards as well as those of the regulators.
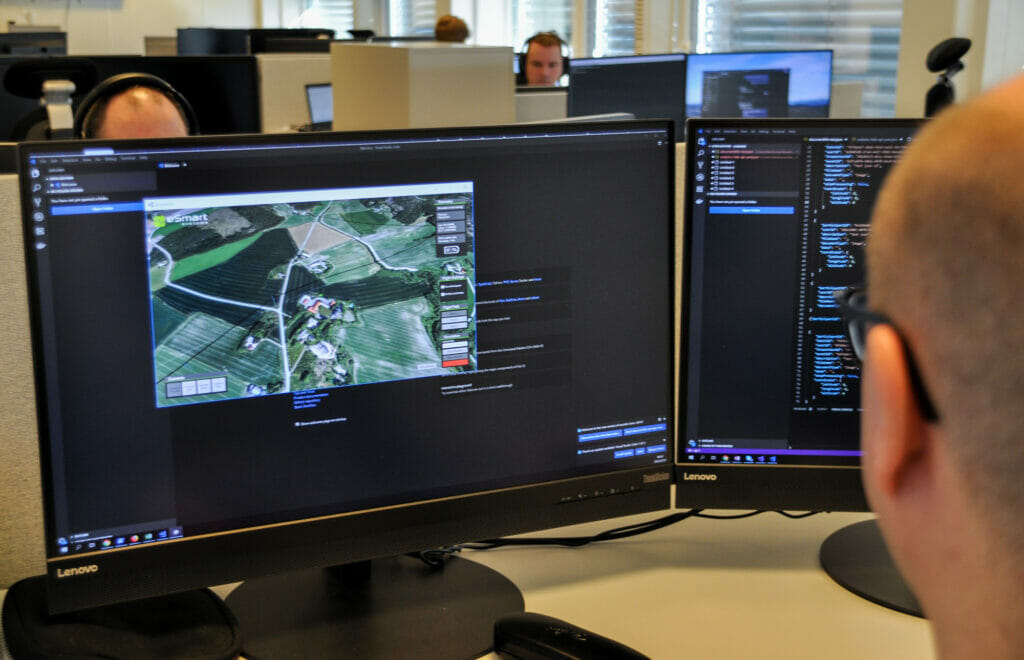
So, before you embark on a virtual inspection initiative, stop and plan. It really can make the difference between an innovation project that gets mothballed, and one that drives efficiency gains, cost savings and automation of your business . We know you are under pressure to reduce your operation and maintenance costs, but remember not all virtual inspections are the same, nor are they the silver bullet for all of your inspection needs. However, they can represent a cost-effective solution to add to your existing toolbox and when done right can reduce your costs, drive efficiency, support your digitalization journey and, most importantly, facilitate safety and reliability improvements.
Contact us today and see how Grid Vision is transforming the way the world’s leading energy providers inspect and maintain critical infrastructure.